钢结构厂房的承载规范是确保建筑安全和功能性的重要标准。这包括了对钢材的强度、连接方式、支撑系统以及抗震设计等方面的规定。这些规范旨在通过合理的设计和施工,使钢结构厂房能够承受预期的荷载,如风压、雪载、自重和设备重量等。规范也要求在设计中考虑到可能出现的各种不利因素,如地震、火灾等极端情况,并采取相应的措施来提高结构的抗震性能和防火能力。钢结构厂房的承载规范是确保其长期稳定使用的关键。
起重机钢结构制造工艺概述
起重机钢结构制造工艺是指在制造起重机过程中,对钢结构的设计、加工、焊接、组装和检测等一系列技术方法和步骤。这些工艺不仅影响起重机的性能和寿命,还直接关系到其安全性。以下是起重机钢结构制造工艺的主要内容:
1. 材料预处理
1.1 原材料装卸与转移
- 使用专用吊具,如吊梁的专用吊卡、夹钳、板钩或磁铁,确保材料的安全装卸。
- 表面处理后立即喷刷薄层硅酸锌防锈底漆,禁止使用在气割与焊接过程中会释放有害气体的防锈油漆。
1.2 钢板矫正
- 对于厚度δ≤14mm、1m波浪度>3mm的板材,以及厚度δ>14mm、1m波浪度>2mm的板材,必须进行矫正整形处理。
- 整形方法包括机床整形或人工冷作整形,人工整形时需在材料上垫δ>8mm的击打垫板。
1.3 型材矫直
- 对于1m直线度>1mm的型材,必须进行矫直处理,方法包括型钢矫直机滚压或油压机顶压。
2. 原材料下料
2.1 下料规则
- 制造负责人需对采购部门提出钢板供应尺寸的要求,以达到科学合理的拼料。
- 主梁、端梁、走台、小车架要统筹考虑,画好排料图再行下料,材料利用率达到95%以上。
2.2 下料方法
- 厚度δ≤12mm的钢板用剪床进行直线形下料。
- 厚度δ>12mm的钢板允许用气割法下料,连续直线长度>500mm时用数控或半自动切割机。
- 壁厚δ≤8mm的圆管与方管须用机床、切管器、砂轮切割机或钢锯下料,壁厚δ>8mm的长大管件可用气割法下料。
3. 钢板拼焊接
3.1 拼接钢板
- 拼接钢板必须在校正合格的金属工作平台面上进行。
- 拼接钢板一般采用自动埋弧焊,板厚δ≤10mm可不开坡口,单面焊接后背面清根焊接。
- 板厚δ=12~22mm开单面(40±5)坡口,背面碳弧气刨清根焊接。
- 板厚δ>22mm开X形(60±5)坡口,钝边焊缝坡口必须用半自动切割机或专用机床制作。
3.2 焊接工艺
- 拼接钢板在拼接缝处校正后先用气体保护焊点焊,点焊后复检对接间隙与对接处平面高低差合格后再行自动埋弧焊焊接。
- 每条对接焊缝两端必须焊接引弧板,拼接钢板必须先拼接宽度,然后再拼接长度。
- 焊接前,离焊缝中心左右各30mm区域内必须将油污、铁锈及杂物打磨清理干净。
4. 焊接制造工艺
4.1 工艺设计
- 母材选择:选择可焊性强的母材,确保大型起重机钢结构焊接与制造的顺利进行。
- 焊接设计:优化坡口设计,规范坡口的形式,达到坡口焊接的标准。
- 工艺控制:控制超出规程以外的偏差、误差,规划钢轨结构焊接制造工艺中的所有尺寸。
4.2 变形控制
- 优化焊接参数,适度调节热输入量,确保熔透的效率,排除焊缝中的缺陷。
- 完善焊接顺序,按照规定的顺序进行焊接,避免出现不必要的焊接缺陷。
- 采用试焊的方式,提前明确钢结构焊接制造的接头性能,实际焊接中避免出现接头缺陷。
5. 检测与质量控制
5.1 结构检测
- 检测内容包括结构变形的控制、火焰矫正变形、制造工艺实例等。
- 检测方法包括目视检查、超声波检测、射线检测等,确保钢结构的质量符合标准。
5.2 质量控制
- 控制焊接制造的温度和热输入值,防止焊接制造中的变形。
- 实现有/无衬垫的准确选择,合理控制焊接制造的温度和热输入值。
- 通过多辊平板矫正机整形或用重砣对其进行反向重力静压整形,防止对接板件焊后角变形。
总结
起重机钢结构制造工艺是一个复杂而精细的过程,涉及材料预处理、原材料下料、钢板拼焊接、焊接制造工艺和检测与质量控制等多个环节。每个环节都需严格按照标准和规范进行,以确保起重机的性能和安全性。通过科学的设计和严格的工艺控制,可以有效提高起重机钢结构的质量和使用寿命。

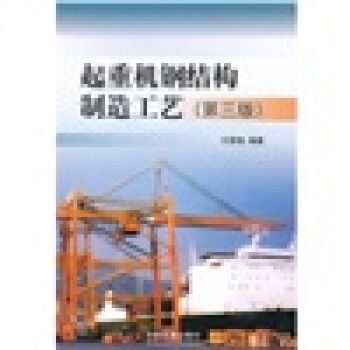
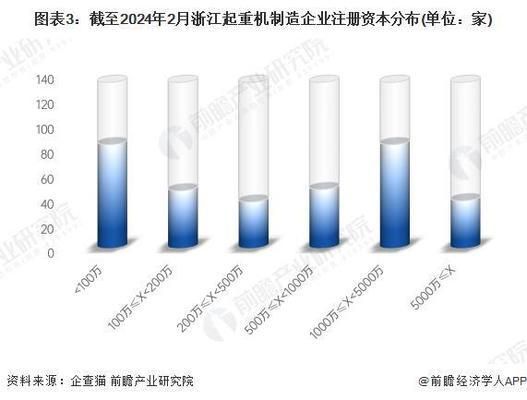
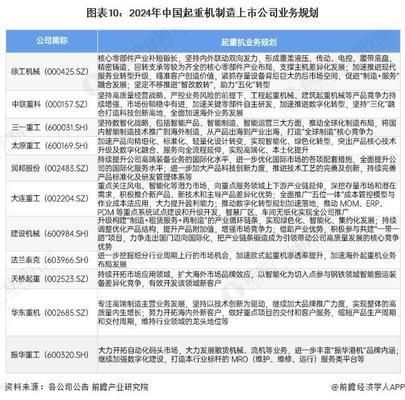
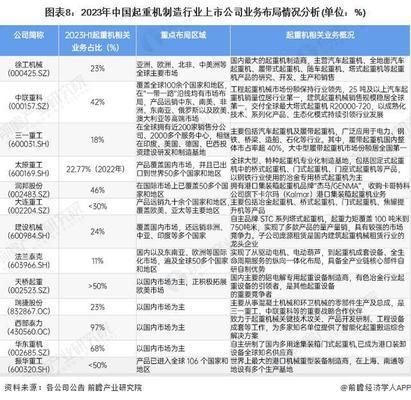